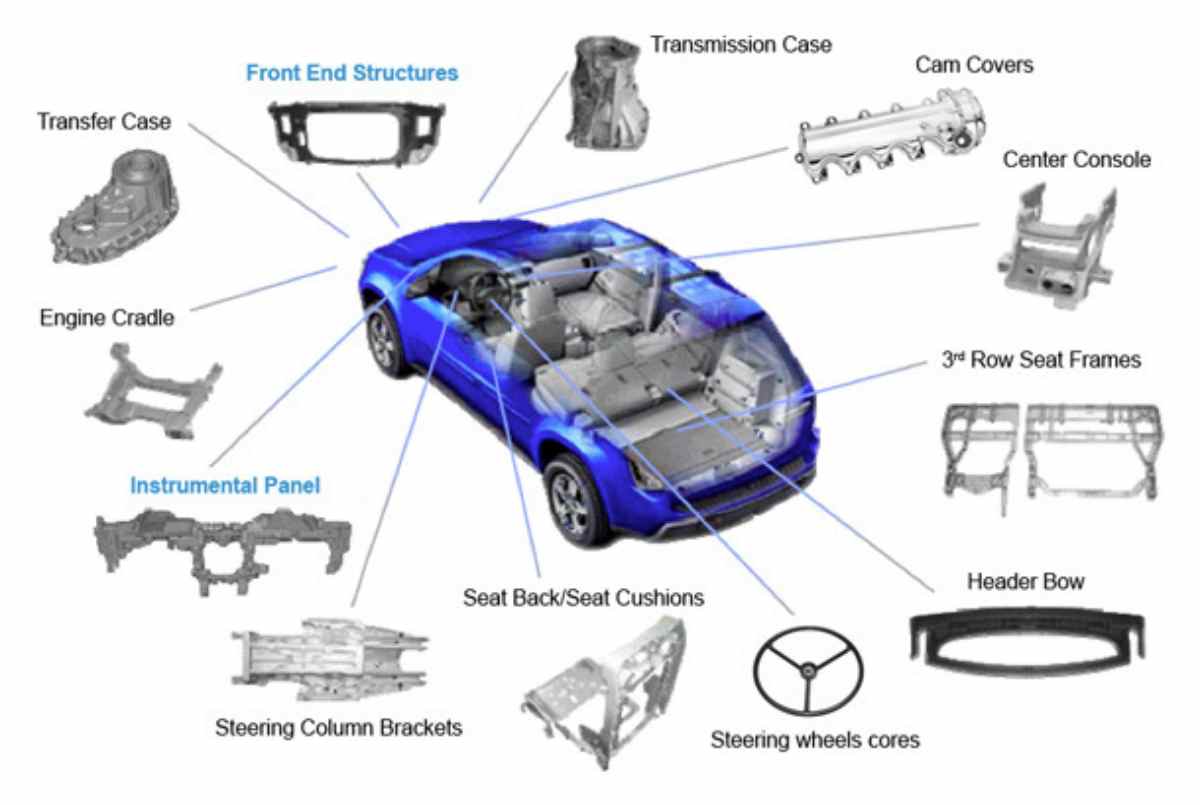
Latrobe Magnesium – Transforming a waste resource into sustainable materials – Latrobe Magnesium’s plant paves the way to a cleaner, high value future. Rockwell Automation Brings the Connected Enterprise to Latrobe Magnesium’s New Sustainable Magnesium Plant
ASX listed company, Latrobe Magnesium (LMG), has produced the first batch of magnesium oxide at its demonstration plant in Victoria’s Latrobe Valley, marking a significant step towards the scaling up of its operations.
Latrobe Magnesium pioneering a patented hydrometallurgical extraction process
LMG is pioneering a patented hydrometallurgical extraction process that converts almost 100% ash – a byproduct of coal-fired power stations – and ferro nickel slag into valuable saleable products like magnesium metal, Supplementary Cementitious Material (SCM), silica, char, iron oxide, and calcium carbonate. One power station alone can supply LMG with enough ash to meet production needs for over 30 years.
Magnesium metal, a critical mineral, is lighter yet stronger than both steel and aluminium, making it an ideal for use in automotive, battery, die casting, electronics, and bioabsorbable stent applications.
“LMG’s ambitious plans required a scalable process and a plantwide control system capable of delivering a truly connected enterprise,” said Anthony Wong, regional director, South Pacific, Rockwell Automation.
Rockwell Automation’s Connected Enterprise® technology integrates plant-level and enterprise networks, securely connecting people, processes, and technologies. This approach leverages smart manufacturing and machine learning to enhance decision-making and streamline connectivity.
Digital transformation from a single point of control Latrobe Magnesium
After evaluating potential solutions, LMG selected Rockwell Automation’s PlantPAx® Distributed Control System (DCS), combined with its Centreline Motor Control System (MCC).
“PlantPAx allows LMG to make faster, more informed process control decisions from a single point of control. The system seamlessly connects and records data, further optimising operations,” said Wong.
The magnesium market is expected to double by 2030. With the growing demand for lightweight vehicles, and as the only new western producer coming onstream. LMG is positioned to meet this demand, with plans to expand operations.
Following successful production at the 1,000 tonnes per annum (tpa) demonstration plant, LMG plans to build a 10,000 tpa plant in the Latrobe Valley, and has completed a Pre-Feasibility Study (PFS) for a 100,000 tpa international mega plant in Samalaju Industrial Park, in the state of Sarawak, Malaysia.
“PlantPAx is designed with scalable, modular architecture that simplifies integration, accelerates time to market, and offers advanced scalable system capabilities like Human-Machine Interfaces (HMI), batch management and data collection.”
“Recent updates to PlantPAx align with digital transformation strategies, enhancing productivity and profitability whilst minimising operational risk.”
“LMG process is groundbreaking. Current magnesium production methods are more than 60% more carbon emission intensive, but this new process eliminates waste products and tailings, offering a more sustainable solution.”
“Given LMG focus on reducing their carbon footprint, Rockwell’s Centreline low-voltage MCCs were a perfect fit. Offering a smaller footprint and, energy-efficient industrial motor control solutions.”
A partnership built on service
Rockwell Automation’s ability to meet tight deadlines and provide transparent timeframes earned the trust of LMG, and the partnership has continued to expand.
“Rockwell’s support to help us meet our production goals has been outstanding. They have gone above and beyond to find solutions and make sure everything works,” said LMG Chief Operating Officer, Ronan Gillen.
“We had a few challenges along the way, which is normal when commissioning a new and novel process. Particularly with integrating equipment suppliers into the overall connected solution we wanted. The Rockwell team went above and beyond to incorporate this equipment and control required into the overall plant control system,” he added.
“We also sourced equipment from overseas that came without any code whatsoever. And the Rockwell team came in and wrote software for it. So that it could be part of the overall connected solution, and our commissioning could proceed. We’ve been extremely impressed with their willingness to solve problems.”
“We are incredibly proud of our future low CO2 process. It can address potentially hazardous waste stockpiles and produce sustainable valuable products with downstream environmental benefits. Whilst providing a critical mineral to the world. We see Rockwell as an important strategic partner as we continue to scale up production.”
About Rockwell Automation
Rockwell Automation, Inc. (NYSE: ROK), is a global leader in industrial automation and digital transformation. We connect the imaginations of people with the potential of technology. To expand what is humanly possible, making the world more productive and more sustainable. Headquartered in Milwaukee, Wisconsin. Rockwell Automation employs approximately 29,000 problem solvers. Dedicated to our customers in more than 100 countries. To learn more about how we are bringing the Connected Enterprise to life across industrial enterprises, visit www.rockwellautomation.com.