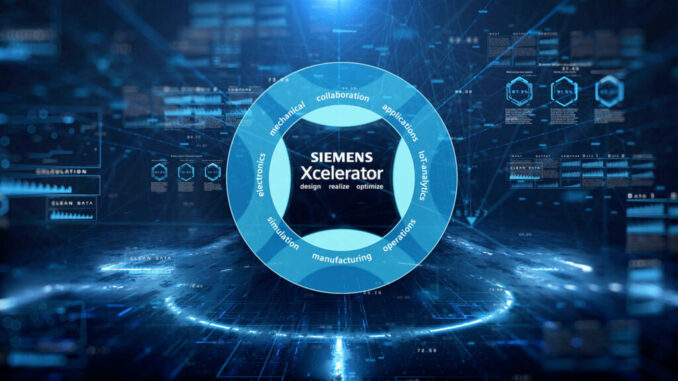
Global technology company Helixx creates unique digital manufacturing ecosystem, has adopted the Siemens Xcelerator portfolio to assist in development of the ‘Factory in a Box’ solution, and enable customers to build mini commercial electric vehicles (EVs) anywhere in the world
- Helixx is leveraging the industry-leading Siemens Xcelerator portfolio of industry software and services to accelerate development of its software-led manufacturing ecosystem
- Facilitates sustainable, commercially viable production of low-cost mini commercial EVs in licensed hubs anywhere in the world
- Siemens ‘digital twin’ technology enables Helixx to design, realise and optimise each stage of factory set-up and manufacturing process
- Development cost and complexity reduced by 20 per cent
- Realtime monitoring of and reaction to digital data at Helixx Mission Control in UK ensures every factory operates at optimum efficiency
Helixx, a new UK-based global technology company, has selected the Siemens Xcelerator portfolio of industry software and services to assist the design, development, validation, delivery, and management of its innovative electric vehicle manufacturing system.
Solutions from the Siemens Xcelerator portfolio have been chosen by Helixx to help realise its goal of supporting sustainable economic development by facilitating rapid manufacture of affordable zero-emission urban mobility solutions worldwide.
In a world-first, the Helixx manufacturing system will empower customers to operate licensed factories, known as Helixx Mobility Hubs, producing a range of mini commercial electric vehicles (EVs) virtually anywhere in the world. The Helixx vehicle range will comprise of CARGO commercial delivery van, TRUCK pick-up for construction sites, and open-body TUK and closed-body RIDE for ride-hailing.
Helixx is responsible for engineering the vehicles and the manufacturing system by which they are produced. While Helixx will manufacture the first vehicles at its concept hub in Oxfordshire and in further pilot hubs in the UK and Singapore producing 10,000 Helixx vehicles a year by 2025 the brand’s mission and ambition go far beyond that.
Steve Pegg, Helixx CEO and Co-Founder: “Helixx has created the world’s first commercially viable system for a factory of the future. But Helixx is not manufacturing a product; it’s a process that can be handed over via a licence to customers anywhere in the world. It enables Helixx partners not just to make a much-needed zero-emission commercial vehicle, but to also run the entire manufacturing system and supply chain autonomously with minimal complexity.
“Collaborating with Siemens and having access to the industry-leading Siemens Xcelerator software portfolio for digital transformation is pivotal to Helixx’s strategy and is a key part of unlocking global growth and supporting our licence holders. Our collaboration with Siemens enables Helixx to develop quickly and amplify efficiency, transparency and quality continuously at every stage of the value chain – from initial factory feasibility study to vehicle end-of-life recycling.”
The Siemens Xcelerator portfolio supports automotive and aerospace OEMs across the globe, and its technology can be seen across major industries from food, energy, transport and marine.
A key advantage of Siemens Xcelerator is the system’s ability to offer a ‘Digital Twin’ for every single element of the Helixx manufacturing ecosystem. Many businesses use digital twins for individual or one-time applications. Creating a digital twin of everything, which entails creating a digital representation of each physical process, component, facility, and environment, will give Helixx a unique advantage through the ability to design, realise and optimise, right from first principles.
Every stage of the process, from each initial customer factory site survey, equipment installation, operator training, supply chain management and manufacturing to retail, productivity, service and maintenance and vehicle end-of-life recycling can be modelled via Siemens’ digital twin technologies and validated ‘in the cloud’ prior to realisation. Once each customer factory, or Helixx Mobility Hub is operational, it will be fully integrated into the Helixx ecosystem and digitally monitored and managed in real-time at Helixx Mission Control in the UK.
Teruyoshi Adachi, Helixx CTO: “Leveraging the Siemens Xcelerator technologies will enable Helixx to weave digital threads through the entire fabric of our business model. Development cost and complexity of not only our mini commercial EVs but the entire end-to-end operational chain has already been reduced by 20 per cent. This simplification unlocks the crucial commercial viability for small, affordable EV manufacturing for our licence holders.
“The technology, which encompasses elements including simulation, collaboration, software systems engineering, accelerated product development, manufacturing, operations, and IoT analytics, effectively enables us to ‘see the future,’ at every stage and on every level of detail from micro to macro. From determining the resources required to build a specific number of vehicles and optimising operator ergonomics to validating the efficiency of processes and the longevity of components, the Siemens Xcelerator portfolio provides a complete and continuous holistic digital overview.”
While Siemens Xcelerator will enable Helixx to capture thousands of digital touchpoints from every mobility hub, all of which will be fed in real-time into Mission Control in the UK, the genius of the Helixx ecosystem is that it removes any element of complexity from the customers and operators in each individual mobility hub. Information sent to the factories and operators will be kept to a functional level via a personalised subscriber experience. Clear, jargon-free instructions will ensure optimum ease and efficiency of production.
Data received in real-time from each Mobility Hub will feed into Mission Control and enable Helixx to instantly spot any quality or production issues, which in traditional automotive manufacturing are only spotted in ‘batch testing’ when it is effectively already too late to resolve, leading to significant cost implications. In addition to using Artificial Intelligence and Machine Learning controls to predict and prevent issues, Helixx will be able to quickly spot efficiency trends and share the knowledge with all the other hubs in the ecosystem to optimise performance and profitability across the entire network as easily as updating the software of an app.
Ben Sheath, VP and Managing Director, UK & Ireland Siemens Digital Industries Software: “The approach being taken by the team at Helixx is an innovative take on building a transportation industry segment from the ground up. Not only do Helixx customers not need to research and develop a physical product, but they are also free from the cost and complexity of developing the associated manufacturing system. Instead, everything is provided for them through the Helixx ecosystem.”
“A modular product from a modular factory is, perhaps, the production architecture needed to realise the factory of the future. We are delighted that Helixx has selected our toolset and chosen to deploy our end-to-end digital twin technologies to help them deliver its ground-breaking vision and production model to reality and we look forward to playing a part in helping it bring in zero-emission mobility and supporting sustainable economic development in emerging markets.”
Be the first to comment